- Marchés
- Produits
- Services
- News
- Outils et Ressources
- A propos de Nexans
- Recherche
- Contactez-nous
- Comparer
- Se connecter
Industrie 1, 2, 3, 4… et 5.0
Nexans réussit le mariage des données et des métiers
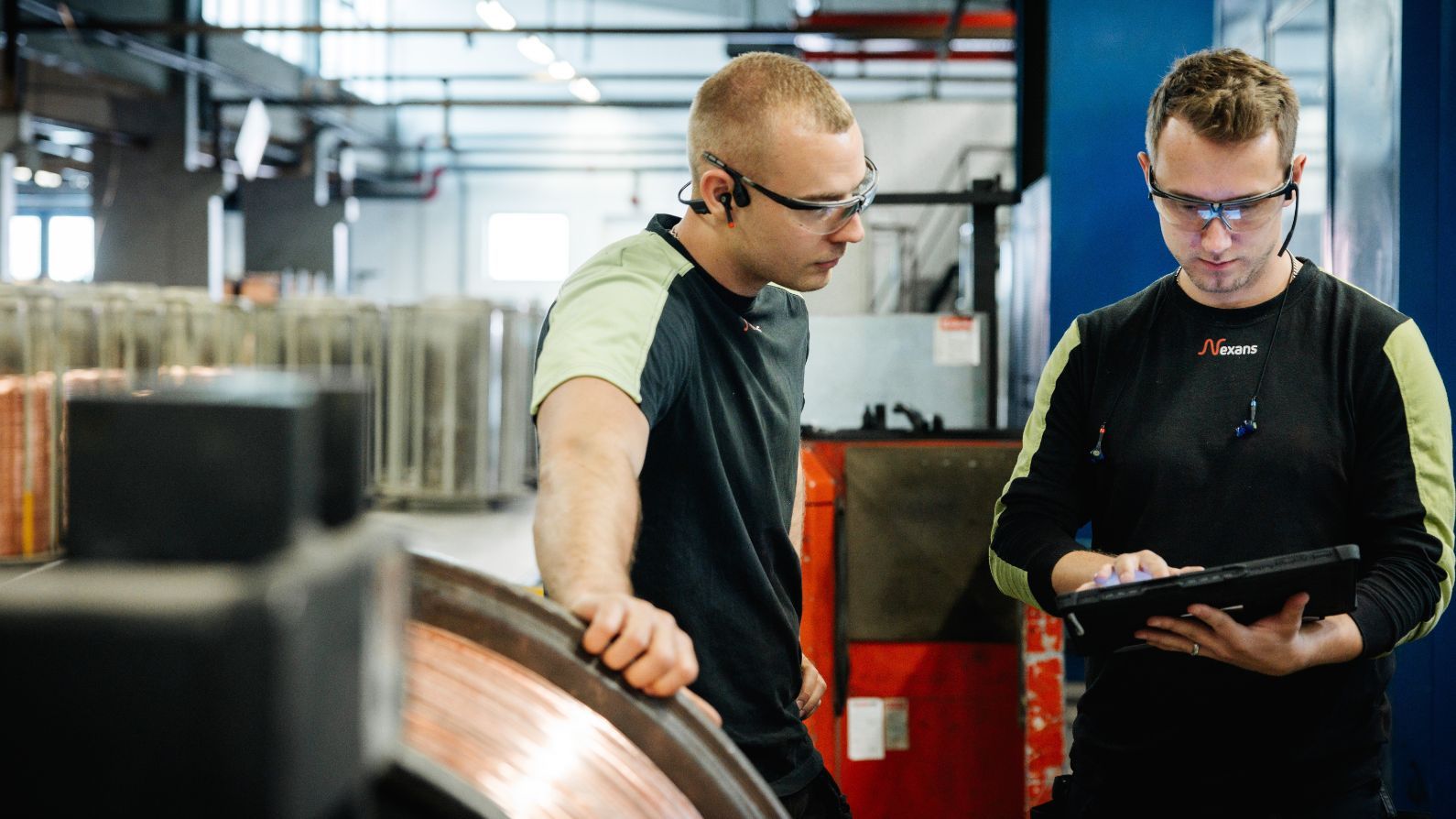
Après le modèle d’une économie sans usine qui a été la marque des trente dernières années, de nombreux pays, tels que les Etats-Unis ou la France, redécouvrent les vertus de la production sur son sol. Une occasion unique pour favoriser le développement d’usines de nouvelle génération, adaptées aux nouveaux enjeux économiques, sociaux et environnementaux. Pour Nexans, qui a toujours fait le choix du local for local, c’est l’opportunité de franchir une nouvelle étape en intégrant son modèle de management exigeant à son outil industriel international qui sera en mode 4.0 dès 2025.
Quand on parle de révolution numérique, on pense d’abord à toutes ces informations qui envahissent notre quotidien, semaine après semaine, pour annoncer la sortie d’un smartphone révolutionnaire, d’un nouveau robot domestique ou les progrès fulgurants de l’intelligence artificielle (IA). Ce n’est que récemment que le sujet s’est invité dans le monde professionnel à travers des débats passionnés sur les effets de l’IA sur les métiers et les tâches susceptibles d’être rapidement automatisées, du programmeur au comptable, du médecin à l’avocat.
Paradoxalement, on parle moins de l’industrie, plus rarement sous le feu des projecteurs, alors même que c’est un sujet majeur en termes d’emplois, d’innovation et de création de valeur, mais aussi de souveraineté depuis que les pays européens ont pris conscience de leur dépendance économique et stratégique à l’occasion de la pandémie de Covid-19 et de la confrontation directe entre la Chine et les Etats-Unis. C’est pourtant dans les usines que se joue une partie importante de l’adaptation de nos économies à la nouvelle donne technologique.
Industrie 4.0, comment l’industrie se réinvente
Ce n’est bien sûr pas une surprise puisque l’évolution des ateliers a toujours été associée à un saut technologique. Un cycle ouvert par deux révolutions industrielles, entamé par la machine à vapeur et les premières usines, amplifié par l’électricité, la machine-outil et la production de masse, et qui s’est poursuivi, dans les années cinquante, par l’électronique et l’automatisation grâce à la programmation, les machines à commande numérique, les robots industriels et les premiers logiciels de supervision.
La quatrième révolution, qui se développe sous nos yeux, s’inscrit directement dans la poursuite d’une informatisation déjà fortement engagée, mais se distingue par son ampleur. Il s’agit tout d’abord de s’appuyer sur un nouveau socle énergétique avec l’ambition de s’émanciper des énergies fossiles qui ont permis les trois précédentes étapes. Il s’agit ensuite d’utiliser au maximum cette nouvelle ressource que constitue les données de l’entreprise en tirant parti du formidable cocktail technologique arrivé à maturité qui combine des infrastructures à très haut débit (fixe avec la fibre et mobile avec la 5G), l’hébergement et le traitement massif des données (Cloud, Big data, IA), la décentralisation de l’intelligence au niveau des objets (IoT) et la disponibilité de nouveaux modes d’interaction homme-machine (réalité mixte, jumeau numérique, avatar).
Cette avalanche d’innovations permet de repenser de manière globale l’ensemble des activités de l’entreprise en intégrant tous les process des activités de production. A tel point que ceci est devenu une priorité pour de nombreuses puissances industrielles. Ce n’est pas un hasard si c’est l’Allemagne qui dès 2011 a lancé le plan Industry 4.0, premier du genre destiné à maintenir l’excellence de son outil industriel. C’est une préoccupation identique qui pousse la Chine à investir dans des usines du futur à forte valeur ajoutée pour conserver sa puissance industrielle et faire face à une pénurie de main-d'œuvre croissante. Une stratégie que la France a adoptée en 2015, avec l’Alliance Industrie du Futur, qui regroupe 32 000 entreprises rassemblées chaque année à l’occasion du salon Global industrie (Lyon, Mars 2023) au cours duquel les équipes de Nexans se sont distinguées en remportant 2 Golden Tech dans les catégories Concepteur et Maker.
Nexans 4.0 à l’horizon 2025
C’est l’expression d’un engagement qui concerne l’ensemble des équipes du groupe Nexans, avec la perspective d’une intégration numérique globale de toutes les dimensions de l’entreprise et de son écosystème pour simplifier les processus, améliorer la performance et être plus réactif, gagner en productivité et en sécurité, limiter les interventions inutiles, anticiper et prévoir les événements (maintenance prédictive, gestion des stocks, satisfaction clients…).
Des investissements qui sont aujourd’hui réalisés par 98% des entreprises françaises interrogées qui déclarent avoir lancé ou mis en route des initiatives Industrie 4.0 (7ème édition du baromètre Wavestone de l’industrie 4.0, en partenariat avec Bpifrance et France industrie). Ces mêmes entreprises qui indiquent que leurs principales motivations sont la recherche de performances industrielles (pour 30% des répondants) et la maîtrise des données (27%). A noter que l’impact écologique et la performance énergétique arrivent depuis cette année en troisième place (15%).
Pour le groupe Nexans, le changement a commencé fin 2020 à l’occasion d’un partenariat avec Schneider Electric qui dispose d’une solide expérience dans la transformation de son propre parc industriel en privilégiant la fiabilité, la productivité, l’amélioration de la disponibilité grâce à la maintenance prédictive, l’efficacité énergétique et la protection contre les cyberattaques. Cela a débuté par des investissements importants sur les sites pilotes d’Autun en France et de Grimsås en Suède, pour être ensuite déployés à huit usines supplémentaires d’ici fin 2023 avec l’objectif de mettre à niveau l’ensemble des 45 usines du groupe sur quatre continents à fin 2025, au rythme de 12 à 15 sites par an.
Ces changements profonds se traduisent par la mobilisation des données du groupe, devenues la véritable matière première de cette nouvelle révolution industrielle. Alors que la part des données utilisées est passée de 5% à 10% entre 2019 et 2023, l’objectif est d’atteindre les 70% d’ici 2026.
“ Nous abordons la transformation digitale du groupe à deux niveaux, par l’intégration des nouvelles technologies dans les opérations d’une part et la création d’un environnement collaboratif d’autre part. ”
Vincent Dessale
Directeur des Opérations de NexansUne mise en œuvre qui assure la connexion des outils de production en utilisant les ressources de l’IoT et de l’IA tout en permettant une prise en main par les collaborateurs grâce au développement de tableaux de bord et d’indicateurs d’aide à la décision, au suivi de la qualité et de la sécurité, en favorisant la réduction des délais d’intervention et de commercialisation.
Pensez à activer les sous-titres de la vidéo en français dans les paramètres
Une révolution : pour quoi faire, ou ce qui change sur le terrain
Au quotidien, c’est bien la manière de travailler qui est amenée à changer. Car les changements ne sont pas que techniques même si les usines font désormais une place de plus en plus grande aux machines connectées et aux robots dopés à l’IA, ainsi qu’aux chariots élévateurs à conduite autonome qui parcourent jour et nuit les centres logistiques. Mais c’est sans doute pour les femmes et les hommes que les changements sont les plus spectaculaires, maintenant qu’ils travaillent dans des ateliers envahis par les écrans, les tablettes et les lunettes connectées.
Un sujet sensible, car une grande partie du succès repose sur l’intégration bien comprise entre les hommes et les machines. C’est justement l’objet de ce que certains appellent l’industrie 5.0, qui consiste à compléter et renforcer cette transformation numérique par une collaboration plus efficace entre les humains et les machines pour que la créativité et le bien-être ne soient pas oubliés.
Une dimension prise en compte dès l’origine dans le projet de Nexans :
- Des tableaux de bord en temps réel permettent de suivre le bon fonctionnement des lignes de production, usine par usine et bientôt pour l’ensemble de l’outil industriel du groupe au niveau mondial. La supervision en temps réel de données permet d’augmenter rapidement les performances industrielles, de renforcer le contrôle de la qualité, mais aussi de réduire les consommations d’énergie et de matières premières, avec une réduction 15% des coûts énergétiques.
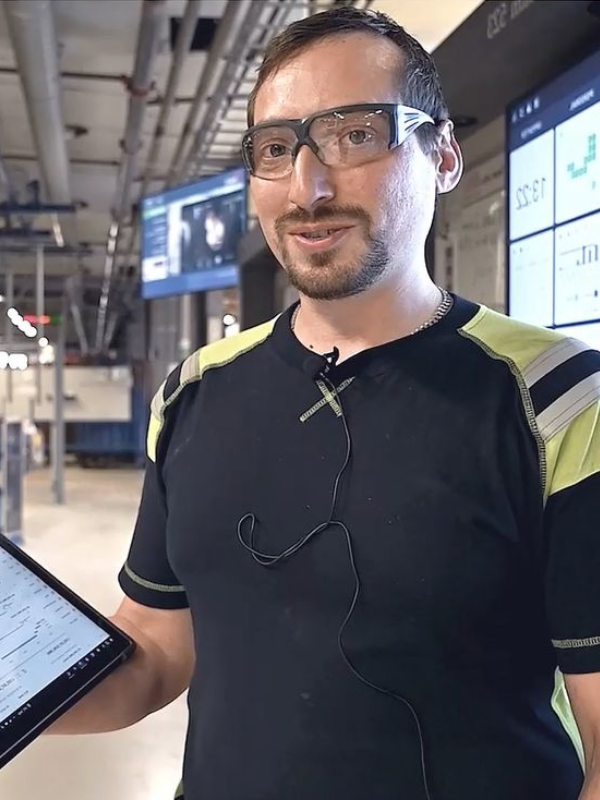
- Un réseau social d’entreprise permet aux opérateurs d’accéder à des modules vidéo et des tutoriels complétés par un forum de discussion. Un atout lorsqu’il s’agit d’échanger de bonnes pratiques et aller rapidement à la solution en adressant directement une question à la communauté en ligne. C’est aussi une façon de garder la mémoire des actions passées qui facilite le partage d’information entre les opérateurs, les équipes et le management, pour plus d’autonomie et de fluidité.
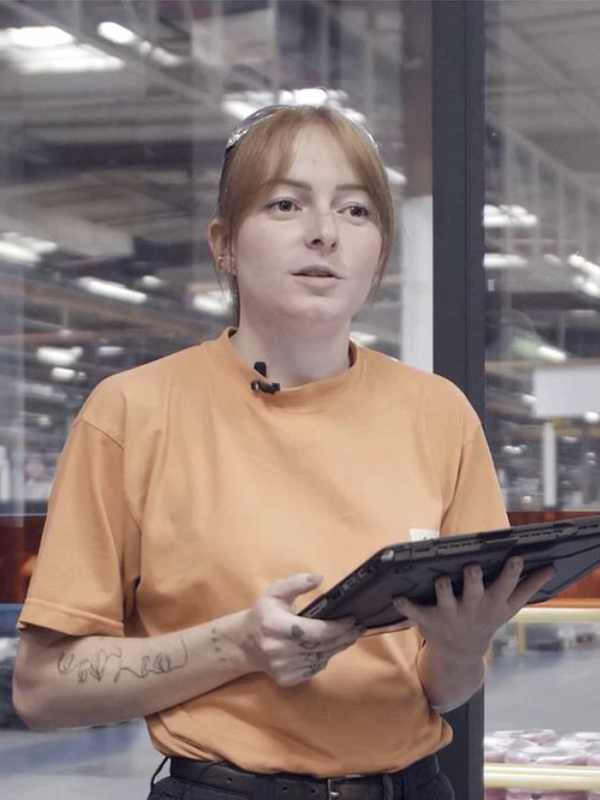
- Les lunettes connectées sont utilisées pour réduire le stress au travail en mettant en relation directe, et à tout moment, experts et opérateurs afin d’aider ces derniers lors de phases de production délicates ou pour résoudre des problèmes urgents de production grâce à la réalité augmentée.
C’est tout l’enjeu de cette étape si importante de s’assurer que la numérisation libère les opérateurs des actions répétitives, pour leur permettre de se consacrer à des tâches à plus forte valeur ajoutée. C’est bien sûr un attrait supplémentaire pour convaincre les jeunes générations, digital native, à s’intéresser à ces métiers et l’occasion d’enrichir le poste de travail, de gagner du temps passé sur les machines, en assurant l’évolution des compétences par des programmes de formation adaptés.
Pour tirer toute la puissance de ce nouveau modèle de gestion des outils de production, il s’agit également d’en assurer l’intégration avec les objectifs stratégiques de l’entreprise. Un effort que Nexans entend pousser le plus loin possible en assurant la cohérence entre le plan industrie 4.0 et le modèle de management, E3, qui sert de socle à la transformation du groupe en alimentant les objectifs de performance économique, de vertu environnementale et d’engagement des équipes.
Lionel Fomperie, directeur de la stratégie industrielle du Groupe Nexans, et Thomas Wagner, directeur de la performance des systèmes d'information de Nexans, donnent un aperçu du programme et expliquent comment les opérations collaborent avec les technologies de l'information et de la communication (IT/OT) pour créer des plates-formes IT/OT et de cybersécurité.
Pensez à activer les sous-titres de la vidéo en français dans les paramètres
Lionel Fomperie, Directeur de la Stratégie Industrielle du Groupe, Chao Li, Ingénieur en Développement Numérique et Olivier Ameline, Directeur de Nexans Excellence Way, nous présentent trois cas d'usage : Unified Operation Cockpit (UOC), MES Performance (Manufacturing Execution System) et SQDCE Digital board : S pour Sécurité, Q pour Qualité, D pour Retard, C pour Coût et E pour Environnement.
Lionel Fomperie, Directeur de la Stratégie Industrielle du Groupe, Chao Li, Ingénieur en Développement Numérique et Olivier Ameline, Directeur de Nexans Excellence Way, nous présentent trois cas d'usage : Unified Operation Cockpit (UOC), MES Performance (Manufacturing Execution System) et SQDCE Digital board : S pour Sécurité, Q pour Qualité, D pour Retard, C pour Coût et E pour Environnement.
Pensez à activer les sous-titres de la vidéo en français dans les paramètres
Le programme de transformation digitale soutient nos opérateurs et leur facilite la vie en facilitant l'accès à tous les documents nécessaires et en soutenant la production à distance.
Découvrez avec Chao Li, Ingénieur en développement numérique, et Mylène Iller, Opératrice de production à Autun, comment la vie des opérateurs est facilitée.
Pensez à activer les sous-titres de la vidéo en français dans les paramètres
Découvrez avec Chao Li, Ingénieur en développement numérique, et Tobias Karlsson, Opérateur de maintenance prédictive à Grimsås, comment la maintenance prédictive a été mise en place dans notre usine suédoise. L'objectif est de surveiller les principaux indicateurs de production tels que la température, la pression, la traction, afin de détecter l'évolution des tendances de ces paramètres.
Découvrez avec Chao Li, Ingénieur en développement numérique, et Tobias Karlsson, Opérateur de maintenance prédictive à Grimsås, comment la maintenance prédictive a été mise en place dans notre usine suédoise. L'objectif est de surveiller les principaux indicateurs de production tels que la température, la pression, la traction, afin de détecter l'évolution des tendances de ces paramètres.
Pensez à activer les sous-titres de la vidéo en français dans les paramètres
Nos sites web
Sélectionnez votre pays pour trouver nos produits et solutions
-
Afrique
- Afrique
- Côte d'Ivoire
- Ghana
- Maroc
- Zone Afrique du Nord
- Amériques
- Asie
- Europe
- Océanie